simond
Western Thunderer
They do look good from the photos - are they full depth?
This is just pushed in. There’s a very thin gap where the weight just doesn’t quite sit on the rim of the wheel.
As you can see, the back in nearly flush and a smear of filler would make it so
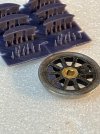
I need to do a set for the 48xx and the Manor.
I wonder about generating a parametric model that allows the weight to be defined by wheel diameter and number of spokes, but I think it might be more trouble than it’s worth as there are other variables required to fully constrain the design.
I think it’s likely to be quicker to just re-save and modify the existing design for each application.