Apart from the "char" issue, the smokebox interior is otherwise done, but there are still plenty of other jobs to do while the boiler is out of the frames.
I really could not put off getting the cladding sorted any longer, especially as the new steam brake piping hugs the firebox end profile quite closely, and I now know exactly where the main steam pipe and blast pipe fixing bolts come through the base of the smokebox.
Inevitably a snag has arisen with those brake feed and exhaust pipes though, and that is entirely a result of my own stubborn determination to keep all the fittings and associated plumbing attached solely to the boiler - in such a way that it will always be possible to separate it from the underframes without having to disconnect a multitude of disparate joints! Fortunately, the original design of the loco has been beneficial in all but two features, namely, the aforementioned brake pipes, one of which has it's union and nut projecting, and both dropping down loosely through holes in the right hand running plate, while the left hand saddle tank balance pipe rather awkwardly reaches the well tank below via a simple notch in the opposite plate!
Leaving aside the latter problem for the moment, the relevant issue of the brake pipes is their small diameter, and the distance from the valve (on the top manifold) to their locating holes in the plate. Lifting the boiler would be easy, but making sure that two slender copper pipes are perfectly aligned - along with ten boiler flange studs - plus ensuring that the motor drive shaft slot engages correctly in the gearbox - and all at the same moment while attempting to maintain a grip on a surprisingly weighty, cylindrical object when putting it back!
There is (supposedly) an answer to everything, but the available solutions are not always entirely acceptable! I have been thinking along the lines of pressing the pipes into actual contact with the boiler cladding for the larger part of the circumference, and using some (almost) hidden, copper pins, drilled and soldered into the back of the pipes, and thence pressed thro the barrel, hoping that such things will only be apparent by very close observation.(?) I am still not sure though!
Whatever approach I finally choose, and soon at that, the cladding must be complete, fully painted and thoroughly varnished beforehand... so off I jolly well need to go...
I doubt that I will ever learn to make life easy for myself - and this task proves it at least twice over again!
Having now (very) permanently fitted the base section of the saddle tank to the boiler barrel means that the cladding sheets have to butt up very tightly under the bottom edge - rather than passing underneath as in the prototype. Careful cutting is not so much the problem here, but for my own comfort, integrity of the glue joint is! It would be such a shame, and downright awkward if the cladding starts to come away along that edge - and end up naturally ballooning outwards? If I had thought more clearly about it at the time, I could easily have cut a shallow rebate on the inner face of the timber rails prior to assembly - but it is all solidly glued and screwed in place now! Some fine tacks, driven well down with a nail punch and covered over with filler will have to suffice.
A result of the original engines being specifically set up (as recently confirmed by other researchers) in the first place for walking control, (horse shunting style driving) all the fittings are on, or readily accessible to the left side, which means that there are several more odd size and shaped holes to cut out in the sheets here. I thought it wise to trim and tape tracing paper on first to ensure every cut would be in the right place:
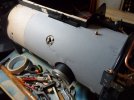
At this point I should mention my second problem:
When I initially made the boiler from a postal tube I knew that the cardboard would have to remain naked for a fair while - at least until some other fittings had been completed. For the sake giving it a modicum of weatherproofing, as well as for appearance, I sprayed it with some automotive type, satin black paint. Readers may recall my intention to use "reclaimed", and apparently nefariously acquired steel sheet for the clothing, but I have since changed my mind, and decided to utilise beautifully fine grained and flexible 0.4mm birch ply instead. I am rather glad that I did from the point of view of cutting out the shapes, but far less so when considering adhesives!
Metal sheet could have been rolled, and thus to a degree, in keeping it's shape would be easier to retain in place, whereas the wood has to be firmly stuck down! Doing so on a pre-painted, and therefore slightly impervious surface, would require some type of "impact" adhesive.
No thanks!
Wood glue spread on wood, or a fibrous, wood based material is partially absorbed and effectively sucks the surfaces smoothly together as it cures... as well as providing some wriggling before it sets.
There was only one thing I could do about it...
It was tedious... dreadfully messy... and terribly spouse annoying... but fortunately practical to peel off the outer, brown paper covering layer - partly aided by the bonding effect of hardened paint!
Unfortunately, it didn't all come off in nice big chunks like the above image though... and I didn't receive much in the way of encouragement when "bits" started migrating either!
It does look nice and smooth already...
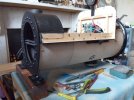
...and hopefully will look even better once fully primed, filled and covered in several coats of gloss!
It is a pity that the LYR never lined the boiler bands on any of these engines since they were rebuilt in the early 1900's... but then again, nowadays I am ever so slightly relieved about that too!!
Pete.