Lyndhurstman
Western Thunderer
Frame At Last
A day of less-than-100% in the health stakes, so I’ve progressed a bit more on the Nickel niceties of the PALBRICK.
The first thing to do was to make the eight triangular supports that keep the ends in place.
Their a bit fiddly, but the plate sits well on the slot designed for it. It’s just a matter of following instructions, really.
The strengthening rib was bent up, and ever so slightly tighter than required.
The plate was then pushed in, and solder paste applied with a sharpened cocktail stick. The assembly was then held against a vee block (yes, I’m a charlatan…) with the end of a needle file, while 25 Watts was applied using the other hand.
(Naff positioning of camera is a skill I’ve had for years).
The result:
After that, the rest of the day has been all about the adjustable end.
The frames were cut from the fret and held in my Bug Hold & Fold to get rid of extraneous tabs and burrs.
the tricky bit here as getting the ‘screws’ to sit upright in the back of the clamping bar. The instructions recommend making the screw 25mm long, and cutting it down to 5mm required after you’ve finished. The Scrooge in me identified that as wasteful, so I went with 10 mm, a pair of tweezers, and some solder paint. I neglected to photo that bit of freehand, so you’ll have to accept it turned out OK (the fact that it was able to sit into the other holes without adjustment spoke volumes).
Once that was done, it was a straightforward matter of putting the other two bits (frame and channel - bent up in the Hold & Fold) together. This was achieved by drilling through holes in the etched components, into a piece of MDF, and putting a couple of 0.9 mm drills in the sockets as alignment dowels
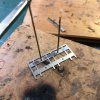
Both parts were tinned, and soldered together. The fit with the clamp was checked again, and the ‘screws’ trimmed to their final length using a suitable mark on the MDF and transferring it to the brass:
The palaver above was repeated for the second clamp bar:
… and that’s where we are.
Cheers
Jan
A day of less-than-100% in the health stakes, so I’ve progressed a bit more on the Nickel niceties of the PALBRICK.
The first thing to do was to make the eight triangular supports that keep the ends in place.
Their a bit fiddly, but the plate sits well on the slot designed for it. It’s just a matter of following instructions, really.
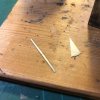
The strengthening rib was bent up, and ever so slightly tighter than required.
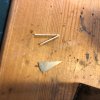
The plate was then pushed in, and solder paste applied with a sharpened cocktail stick. The assembly was then held against a vee block (yes, I’m a charlatan…) with the end of a needle file, while 25 Watts was applied using the other hand.
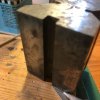
(Naff positioning of camera is a skill I’ve had for years).
The result:
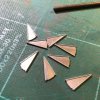
After that, the rest of the day has been all about the adjustable end.
The frames were cut from the fret and held in my Bug Hold & Fold to get rid of extraneous tabs and burrs.
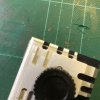
the tricky bit here as getting the ‘screws’ to sit upright in the back of the clamping bar. The instructions recommend making the screw 25mm long, and cutting it down to 5mm required after you’ve finished. The Scrooge in me identified that as wasteful, so I went with 10 mm, a pair of tweezers, and some solder paint. I neglected to photo that bit of freehand, so you’ll have to accept it turned out OK (the fact that it was able to sit into the other holes without adjustment spoke volumes).
Once that was done, it was a straightforward matter of putting the other two bits (frame and channel - bent up in the Hold & Fold) together. This was achieved by drilling through holes in the etched components, into a piece of MDF, and putting a couple of 0.9 mm drills in the sockets as alignment dowels
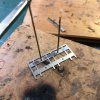
Both parts were tinned, and soldered together. The fit with the clamp was checked again, and the ‘screws’ trimmed to their final length using a suitable mark on the MDF and transferring it to the brass:

The palaver above was repeated for the second clamp bar:
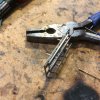
… and that’s where we are.
Cheers
Jan