Giles
Western Thunderer
The nice photo above of laser cut rods is worthy of note because - not only does it show a nice job - but it shows the start and stop of the cut off the main part, which enables a clean cut and Kerf all around, instead of the usual indentation to the profile uou get when the cut starts on the job itself.
SCISS was certainly a good company for water-jet, they're owned by railway enthusiasts (coincidentally). I had some 16mm frames and motion cut by them years ago, and very nice too......
LASER can harden the edge of steel profiles, which takes its toll on your files etc.... on bigger stuff (non railway related) we would dress edges down with a flap wheel in a grinder to clean the job up.
If soldering, use Cool Paste to stop previous joints from remelting. It's remarkably effective, verging on magic.
SCISS was certainly a good company for water-jet, they're owned by railway enthusiasts (coincidentally). I had some 16mm frames and motion cut by them years ago, and very nice too......
LASER can harden the edge of steel profiles, which takes its toll on your files etc.... on bigger stuff (non railway related) we would dress edges down with a flap wheel in a grinder to clean the job up.
If soldering, use Cool Paste to stop previous joints from remelting. It's remarkably effective, verging on magic.
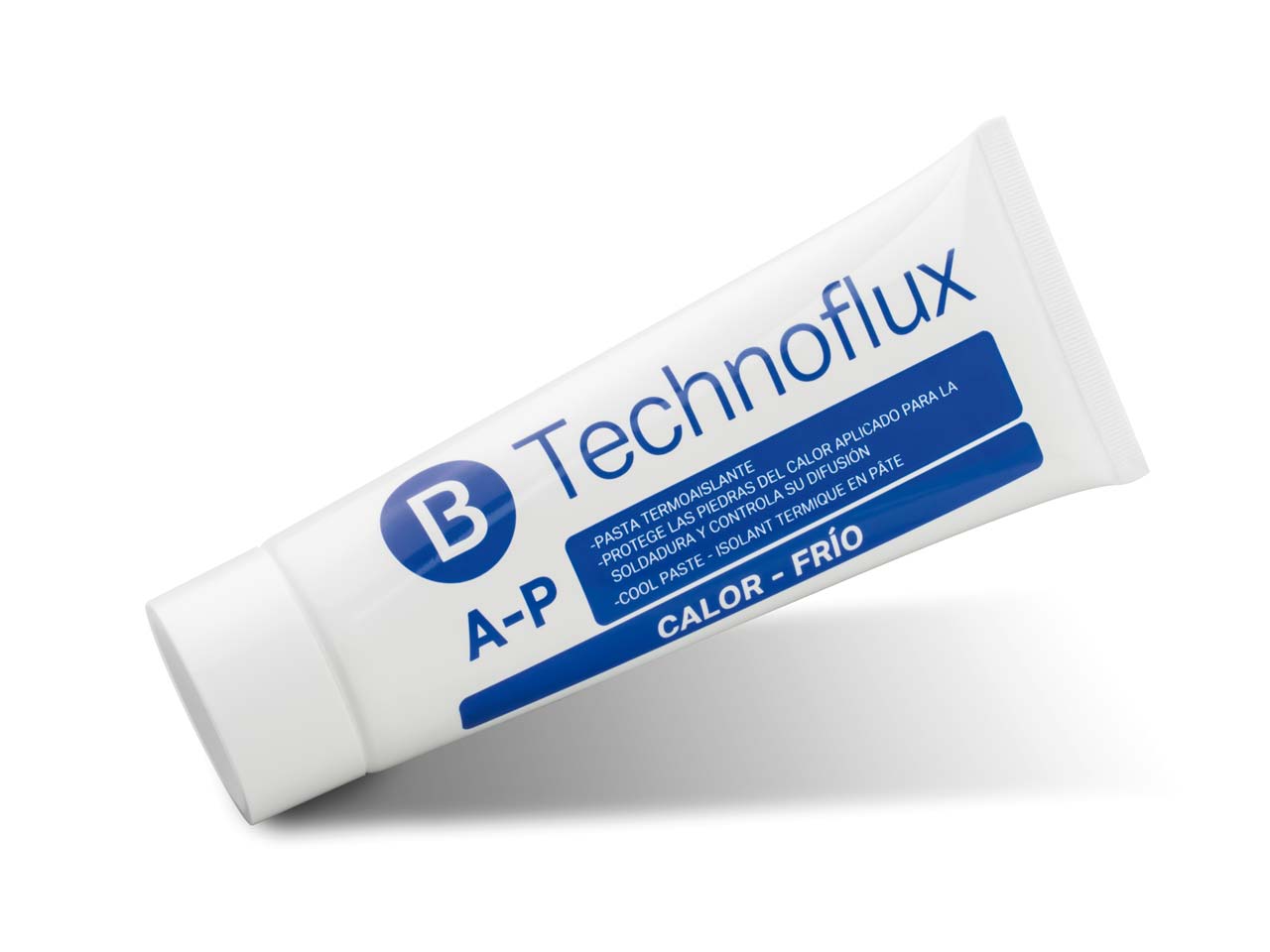
Technoflux Heat Insulating Paste 120ml
Technoflux cool paste is a heat insulation paste used to protect areas not requiring heat when soldering e.g. stones areas of metal o.. - Product Code : 999 AAH
www.cooksongold.com