B462076 - PALBRICK B
Lyndhurstman
Western Thunderer
The Jig Is Up....
side down (cue Diana Ross).
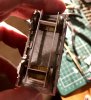
Some wheelbase setting work, via a(nother) home made jig. This one is a direct cadge from the one in the Underframes chapter of John Hayes’ ‘4mm Wagon’. Every wagon buff should have a copy, I think. Just to marvel at the artistry on display. And the attention to detail is second to none (second to monks, too). I love that book. I love that level of skill. I love that level of commitment and passion, writ large in tiny boxes.
Anyway... here’s the Watkins Wharf wheelbase setting jig - two bits of 20 thou joined in a box. Slotted fir 2.0mm axles. The most difficult part was making the initial holes; I tend to start at 0.5mm and go up in 0.5mm increments. This stops the drill catching, I find. And there’s something very soothing about drilling Plasticard... no? Just me then... I put the stretchers in after, pushing them tight against the axles before glueing.
It’s all progress. Not leaps and bounds. More of a determined limp into the headwind. But we’re used to that. As long as the thing we’re getting is somewhere.
Cheers
Jan
side down (cue Diana Ross).
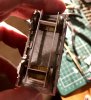
Some wheelbase setting work, via a(nother) home made jig. This one is a direct cadge from the one in the Underframes chapter of John Hayes’ ‘4mm Wagon’. Every wagon buff should have a copy, I think. Just to marvel at the artistry on display. And the attention to detail is second to none (second to monks, too). I love that book. I love that level of skill. I love that level of commitment and passion, writ large in tiny boxes.
Anyway... here’s the Watkins Wharf wheelbase setting jig - two bits of 20 thou joined in a box. Slotted fir 2.0mm axles. The most difficult part was making the initial holes; I tend to start at 0.5mm and go up in 0.5mm increments. This stops the drill catching, I find. And there’s something very soothing about drilling Plasticard... no? Just me then... I put the stretchers in after, pushing them tight against the axles before glueing.
It’s all progress. Not leaps and bounds. More of a determined limp into the headwind. But we’re used to that. As long as the thing we’re getting is somewhere.
Cheers
Jan
Last edited: