michael mott
Western Thunderer
Hi Jon
Thanks for the interest. the punches are really simple to make out of silver steel or Drill rod as it is called on this side of the pond. I suppose one could also use old broken drill bits.
however the method that I have been using is to use a diameter that is larger than the punch that I need and use the appropriate centre drill to begin then drill out the bore to 15 -20 thou smaller than the finished diameter of the punch. Then turn down the diameter until till it is the diameter that I need. I use a bit of 1200 wet and dry to polish up the inside and the outside which because of the right centre drill gives a bevel edge that is sharp enough for this purpose, and then I heat the punch end about 3/4 inch up from the tip of the punch to cherry red and let the heat transfer down to the cutting edge and when it is red quench it in some vegetable oil. re-polish I have not found the need to temper these punches. They don't seem to suffer much in the way of wear when used on the normal cutting mats.
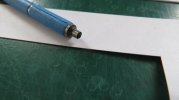
after punching a full hole the punching needs to be removed right away, because the depth is not deep.
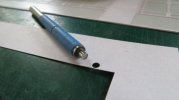
I use a small tool that I also use to catch small parts when parting off on the lathe.
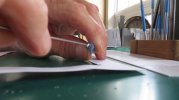
the reason for cutting out the rounded corners afterwards is because it is easier to be more accurate positioning the punch. The blue masking tape simple makes the punch less slippery to hold. and there is no need to interrupt the flow because the half moon simply drops out 99% of the time.
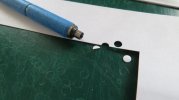
last an assortment used for the sides.
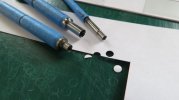
I hope this helps.
Michael
Thanks for the interest. the punches are really simple to make out of silver steel or Drill rod as it is called on this side of the pond. I suppose one could also use old broken drill bits.
however the method that I have been using is to use a diameter that is larger than the punch that I need and use the appropriate centre drill to begin then drill out the bore to 15 -20 thou smaller than the finished diameter of the punch. Then turn down the diameter until till it is the diameter that I need. I use a bit of 1200 wet and dry to polish up the inside and the outside which because of the right centre drill gives a bevel edge that is sharp enough for this purpose, and then I heat the punch end about 3/4 inch up from the tip of the punch to cherry red and let the heat transfer down to the cutting edge and when it is red quench it in some vegetable oil. re-polish I have not found the need to temper these punches. They don't seem to suffer much in the way of wear when used on the normal cutting mats.
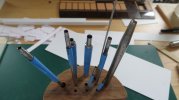
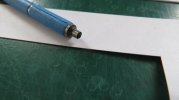
after punching a full hole the punching needs to be removed right away, because the depth is not deep.
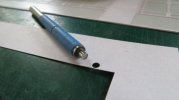
I use a small tool that I also use to catch small parts when parting off on the lathe.
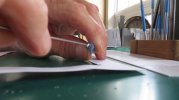
the reason for cutting out the rounded corners afterwards is because it is easier to be more accurate positioning the punch. The blue masking tape simple makes the punch less slippery to hold. and there is no need to interrupt the flow because the half moon simply drops out 99% of the time.
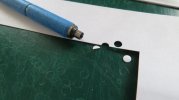
last an assortment used for the sides.
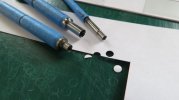
I hope this helps.
Michael