Dave
Western Thunderer
I tried that but with Loctite instead of Araldite. It actually worked and I managed to hand file the flare.Oh no!
You could try araldite to put it back together and some rod to line it up?
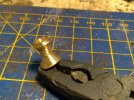
It's a chimney, but not the right chimney. A forum member has very kindly offered to make me a proper one.
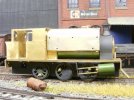
1814 had at least 3 chimneys in its life. Firstly the short one, then what appears to be a taller Manning Wardle chimney and finally a tall replacement that was its last and appears to have been fitted to either a new boiler or at least a new, welded, smokebox.
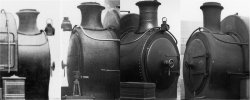
The last but one photo, with the cylinders and slide bars on, ought to have come after this one.
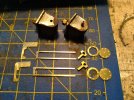
The cylinder ends and motion brackets are made from 18 thou. hard brass, the slide bars from 30 thou. nickel silver and the strange bits are the piston glands or whatever. The extra bit is there to give something to hold in pliers whilst filing them to be a good fit in the slide bars. It was sawn off after the part was soldered into the slide bars.
The slide bars are made overly long so that the part on the left sticks out beyond the motion bracket and keeps the bars to gauge until they are soldered into the motion bracket. The excess is then sawn off, leaving two bars soldered in and lined up.